This past weekend i got bored and decided to undertake making a barrel nut wrench for my YHM barrel nut. Before anyone says you can just buy one for cheaper i know this and to be honest i didnt spend more than 8$ making this. I already had the tools/metal and only have my time in it. I found where another member had a CAD drawing of their version of a barrel nut wrench and i just tweaked it a little.
CAD file for barrel nut wrench
Below is the basic drawing that i printed in 1:1 out of CAD and taped it onto my piece of metal (.120") and used a center punch i ground to a point to mark the centers of all the holes.
What i used for the studs was some 10-32 Socket head screws that had a shank on them similar to these
After i drilled & tapped the holes to 10-32 i put a dab of JB weld on the threads and threaded the screw all the way in until it shanked out then cut off the head and most of the threads but left a little on there and covered with JB weld too.
The larger holes i used a 1 1/16" Hole saw then cleaned up the edges.
I didnt want to just cut a square for the torque wrench as i was worried it wouldnt turn out well so i got a cheap 13/16th socket at my local tool wholesale store and cut the socket end off & ground the chrome off for better welding & fit. It was a snug fit after that and had a friend tig weld it in place.
Cleaned up & rounded all the edges then applied some cold blue i had laying around along w/ a light coat of oil. She was done and the finished product.
Before the socket was welded in place & not rounded.
Before cold blue but shows the back of the screws, ill redo the JB weld too because a little got removed during welding, grinding.
CAD file for barrel nut wrench
Below is the basic drawing that i printed in 1:1 out of CAD and taped it onto my piece of metal (.120") and used a center punch i ground to a point to mark the centers of all the holes.
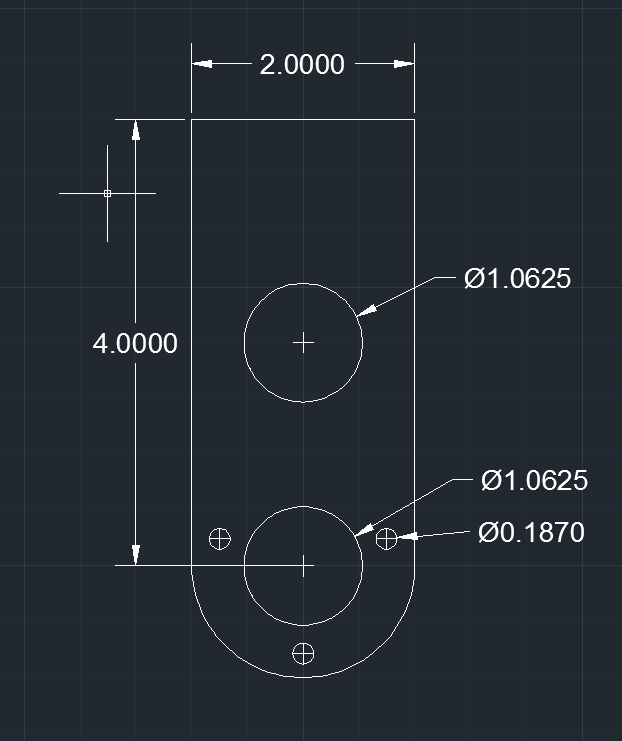
What i used for the studs was some 10-32 Socket head screws that had a shank on them similar to these
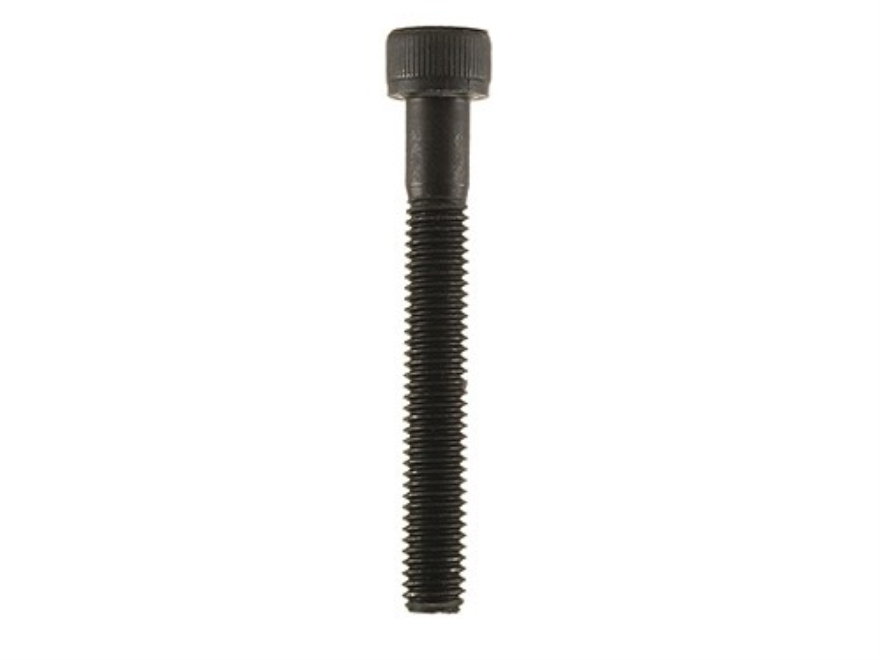
After i drilled & tapped the holes to 10-32 i put a dab of JB weld on the threads and threaded the screw all the way in until it shanked out then cut off the head and most of the threads but left a little on there and covered with JB weld too.
The larger holes i used a 1 1/16" Hole saw then cleaned up the edges.
I didnt want to just cut a square for the torque wrench as i was worried it wouldnt turn out well so i got a cheap 13/16th socket at my local tool wholesale store and cut the socket end off & ground the chrome off for better welding & fit. It was a snug fit after that and had a friend tig weld it in place.
Cleaned up & rounded all the edges then applied some cold blue i had laying around along w/ a light coat of oil. She was done and the finished product.
Before the socket was welded in place & not rounded.
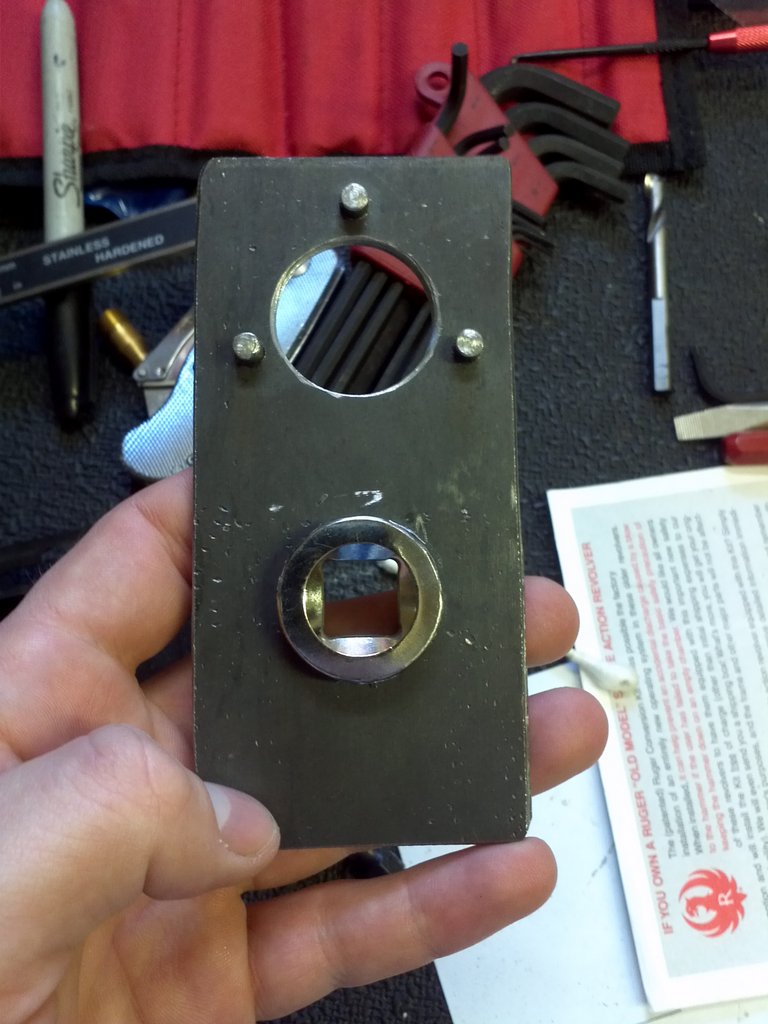
Before cold blue but shows the back of the screws, ill redo the JB weld too because a little got removed during welding, grinding.
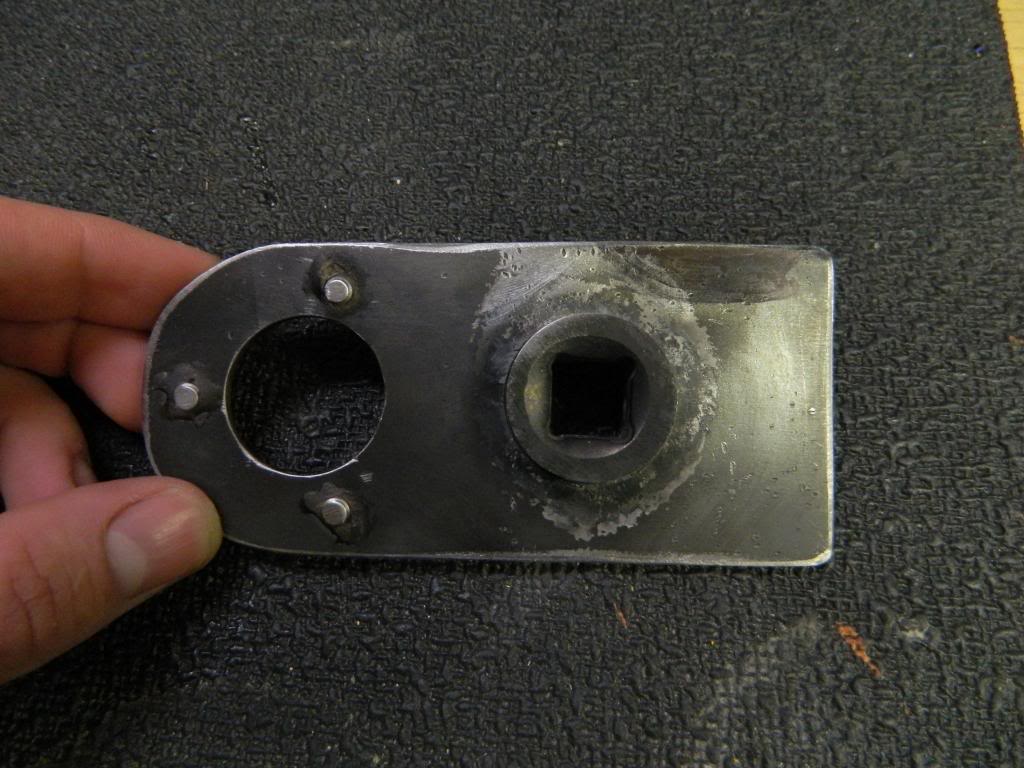
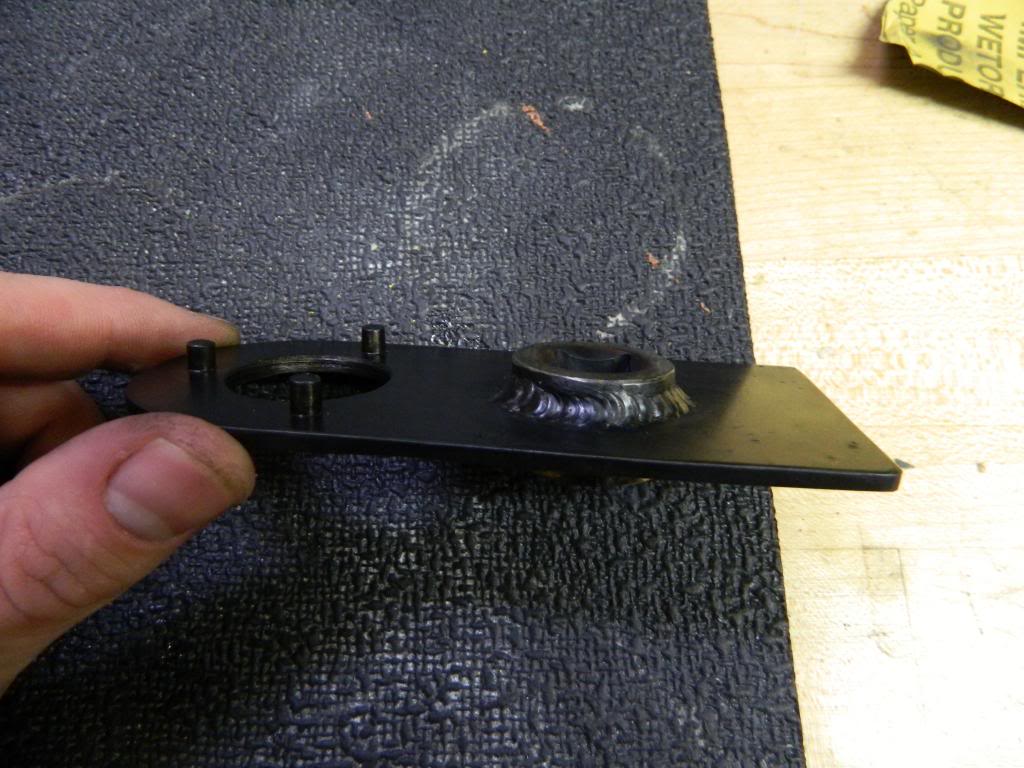
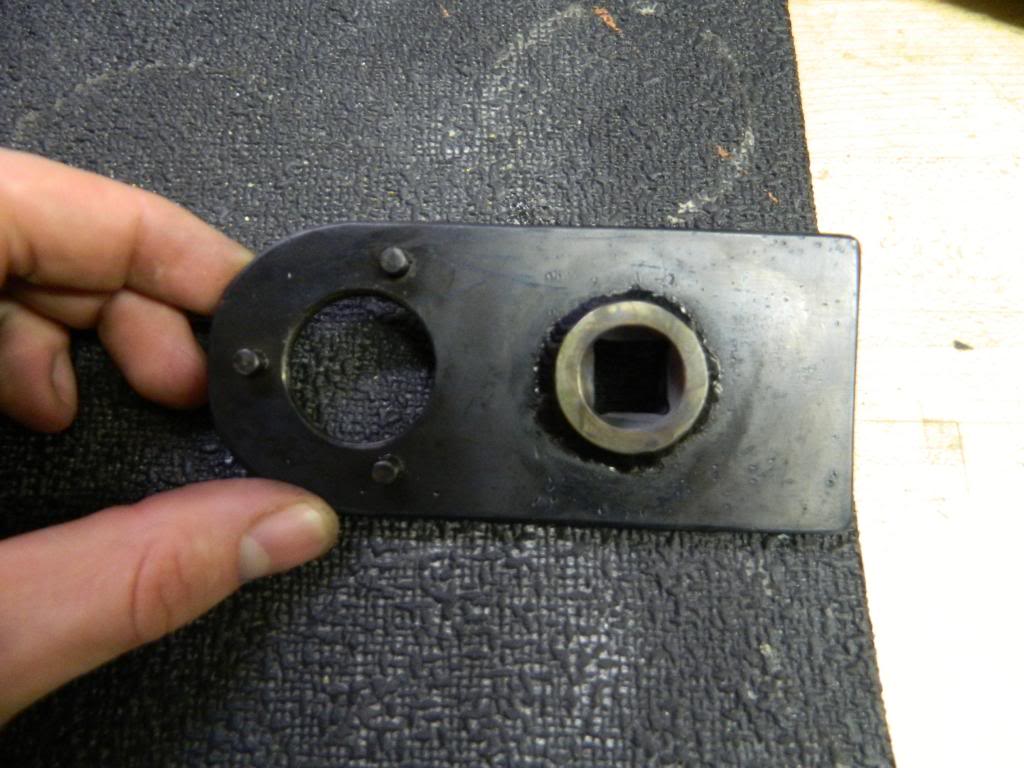
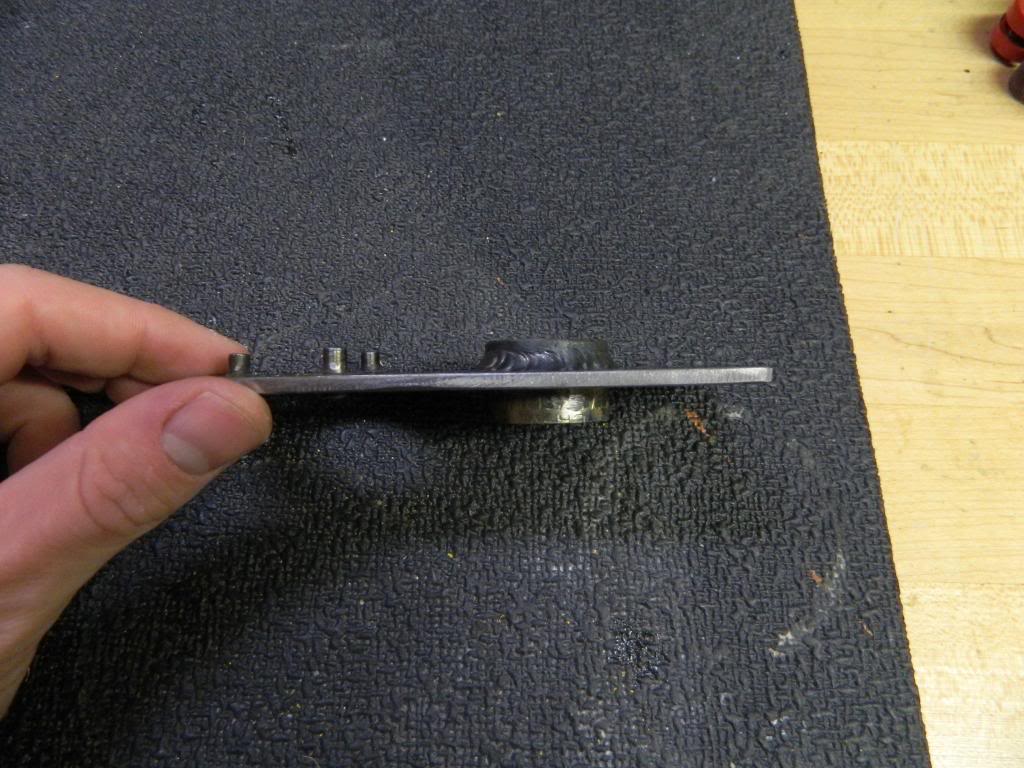
Last edited: